滚动轴承材料及热处理之“热处理技术进展”
滚动轴承材料及热处理之“热处理技术进展”
- 2020/5/20 14:49:28
1、常规淬回火
高碳铬类轴承钢通常采用马氏体淬回火,国内外进行了大量的研究,近年来根据轴承应用工况,提出了一些针对性的研究与应用。
ЧЕРМЕНСКИ.О.Н研究了不同温度回火后硬度对轴承性能的影响。当轴承载荷产生的接触应力超过σn0(σn0=2.57σ0,σ0为在单向拉伸或压缩时开始塑性变形的应力,取σ0.005),在计算可靠性要求不高的轴承寿命时,硬度在58~64HRC范围内寿命的变化可以忽略不计。对于精密重载部件用球轴承,不允许在工作过程中因微塑性变形积累而使套圈沟道尺寸发生变化,最好采用高温回火(200~250 ℃);对一般用途的轴承,最好的回火温度不是现在的150~160 ℃,而是提高到170~180℃,不降低寿命且承载能力有所提高。
日本学者樋口博和对汽车变速箱轴承提出了3种长寿命热处理措施:1)增加残余奥氏体以提高滚动疲劳寿命(TM处理),对高碳铭轴承钢进行淬火时,通过提高淬火温度增加残余奥氏体含量。2)提高回火软化抗力(TA处理),进行碳氮共渗时,由于氮在表层的扩散导致残余奥氏体量增多,此外由于氮的固溶,回火软化抗力上升,进而提高疲劳寿命。3)晶粒微细化(FA处理),使钢材的晶粒尺寸微细化,缩小到传统材料晶粒尺寸的50%以下,以提高疲劳强度,并组合碳氮共渗处理实现进一步长寿命化。
GHEORGHIES.C,STEFANESCU.I.I对高碳铬轴承钢在磁场中进行淬回火后的组织和性能进行了研究。在磁场中进行热处理时,马氏体晶粒变小且组织均匀,残余奥氏体减少,硬度可提高(1~2)HRC,抗弯强度提高50%,疲劳可靠度提高(承载时组织不易变化)。
对高碳铬轴承钢在淬火后进行深冷处理可以提高耐磨性。1)在深冷处理过程中,大量的残余奥氏体向马氏体转变,在磨损过程中向碳化物提供强大的支承并抑制其脱落,阻止大的麻点形成;2)由深冷处理产生的细小碳化物析出并均匀分布,也是耐磨性提高的原因,深冷处理试样中碳化物的分布比那些没进行深冷处理的均匀,且碳化物体积分数更高;3)深冷处理提高了马氏体的转变率,使合金基体组织细化,从而达到细晶强化效果,有助于耐磨性的提高。对100Cr6试样淬火后进行-186 ℃×24 h的深冷处理,并进行200 ℃回火,与未进行深冷处理相比,试样的硬度提高18%,耐磨性提高37%。
BARTARYA.G,CHOUDHURY.S.K对热处理工艺参数对钢球滚动疲劳寿命的影响进行研究,860 ℃加热后具有合适的未溶碳化物数量及原奥氏体晶粒,进行160 ℃回火后可获得较高的疲劳寿命。钢球的抛丸强化可以减少钢球加工和轴承装配时的表面损伤,但疲劳寿命会下降,振动噪声会增加。
BRYAN.A等研究了滚动接触疲劳过程中初始残余应力对轴承钢材料性能的影响,对M50制大钢球(28.6~41.3 mm)进行机械处理,在表面下700 μm内得到初始残余压应力(-400 MPa),与未机械处理的球相比,初始残余压应力延缓了钢中微观塑性变形硬化和组织变化(次表面黑色腐蚀区及白色条带的出现),有利于提高接触疲劳寿命。
在常规淬火设备方面,主要是在减小淬火变形,提高淬火后材料的组织和硬度均匀性方面进行研究应用。如近年来在国内推行的高压气淬技术,可明显减小淬火变形,且节能环保;连续式盐浴淬火设备在国内得到越来越多的应用,通过调节盐浴含水量,可控制冷速,适用于不同的零件尺寸,保证最小的淬火变形及最大的硬度均匀性,且通过有效的热回收利用装置回收清洗液中的盐,实现少无排放和低能耗。
另外,随着热锻套圈技术的进步,提高了毛坯精度,普遍使用热回收氮基保护气氛球化退火,降低了能耗和工件脱碳。
2、贝氏体淬火技术
张福成等对近年来贝氏体淬火技术进行了详细的综述。与马氏体组织相比,在马氏体转变起始温度(Ms点)以上进行等温淬火处理获得的下贝氏体组织在保留高硬度的同时,兼具更高的韧性,同时表面为残余压应力,使得贝氏体淬火轴承在某些应用领域具有优异的疲劳性能,因此适用于装配过盈量大、服役条件差的轴承,如承受大冲击载荷的铁路、轧机、起重机等轴承,润滑条件不良的矿山运输机械或矿山装卸系统、煤矿用轴承等。高碳铬轴承钢贝氏体等温淬火工艺已在铁路、轧机轴承上得到成功应用,取得了较好效果。
近年来新发现的纳米贝氏体组织,也称为硬贝氏体组织、低温贝氏体或超级贝氏体组织,在保留与马氏体相当硬度的同时,具有比常规下贝氏体组织更高的韧性和相当的表面残余压应力,具有更加优异的耐磨性和滚动接触疲劳性能,纳米贝氏体钢在材料设计、微结构调控等基础理论研究方面得到了快速发展,推动了其在轴承制造领域的应用,在轴承上应用具有的巨大潜力。
在20世纪90年代,SKF等公司开展纳米贝氏体用钢开发,如SKF的755V,通过特殊的等温淬火得到更均匀的纳米下贝氏体,硬度增加的同时韧性也提高了60%,耐磨性提高了3倍。处理的套圈壁厚超过100 mm,近期将其应用于高铁轴承。国内近十几年也开展了纳米贝氏体技术的研究,如张福成等团队开发的含Al,Si的全淬硬钢及渗碳钢,经过贝氏体淬火后获得纳米贝氏体,接触疲劳寿命较普通轴承钢及渗碳钢分别提高1倍、2倍以上。
在国内,纳米贝氏体轴承技术的应用仍有一些问题,最突出的问题是等温处理时间过长,急需缩短热处理工艺周期的方法。另外,服役过程中残余奥氏体的转变及其引发的尺寸稳定性问题,纳米贝氏体组织在轴承服役过程中的组织演变规律及对服役寿命的影响,纳米贝氏体轴承更适用的工况等,均有待深入研究。
3、碳氮共渗
高碳铬轴承钢的碳氮共渗处理是在添加了5%~15%丙烷和丁烷的渗碳气氛中加入含氮介质(如氨气),将碳和氮同时渗入扩散到轴承钢中的处理技术。由于在材料表层扩散的氮元素会使奥氏体变得稳定,因此淬火后残余奥氏体量增多,而且通过氮元素的固溶作用提高了抗回火软化性,亦增加了滚动疲劳寿命。
KARTHIKEYAN.R等对52100钢实施的碳氮共渗处理工艺及处理后的组织、硬度等进行了详细的研究。工艺曲线、成分分析、显微组织、硬度分别如图1—图3所示。碳氮共渗温度一般在A1以上,温度越高则渗速越高,但渗后晶粒越粗,氮含量越低。碳氮共渗后除未溶碳化物外,还有大量细小的氮化物、碳氮化物,提高了硬度和耐磨性。另外渗层组织中有高含量的残余奥氏体(20%以上)。因大量残余奥氏体的存在,渗后低温回火的硬度与未渗的相近,但在较高温度回火后,渗层表面硬度明显高于未渗件(如300 ℃回火后,渗后硬度为63.6HRC,未渗的仅58HRC)。
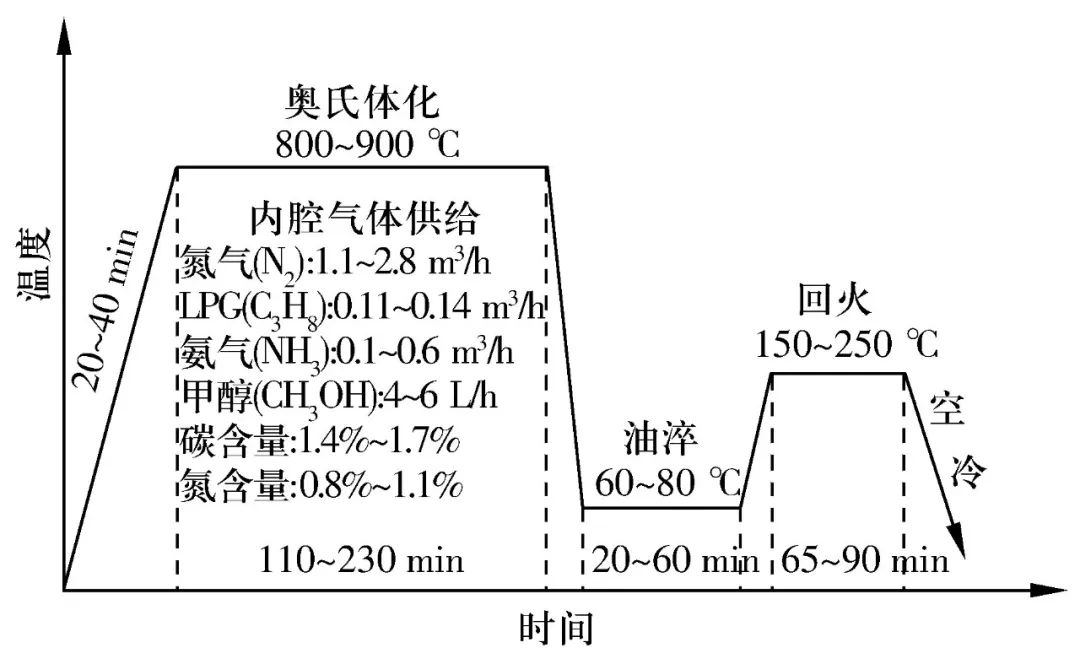
图1 碳氮共渗工艺曲线
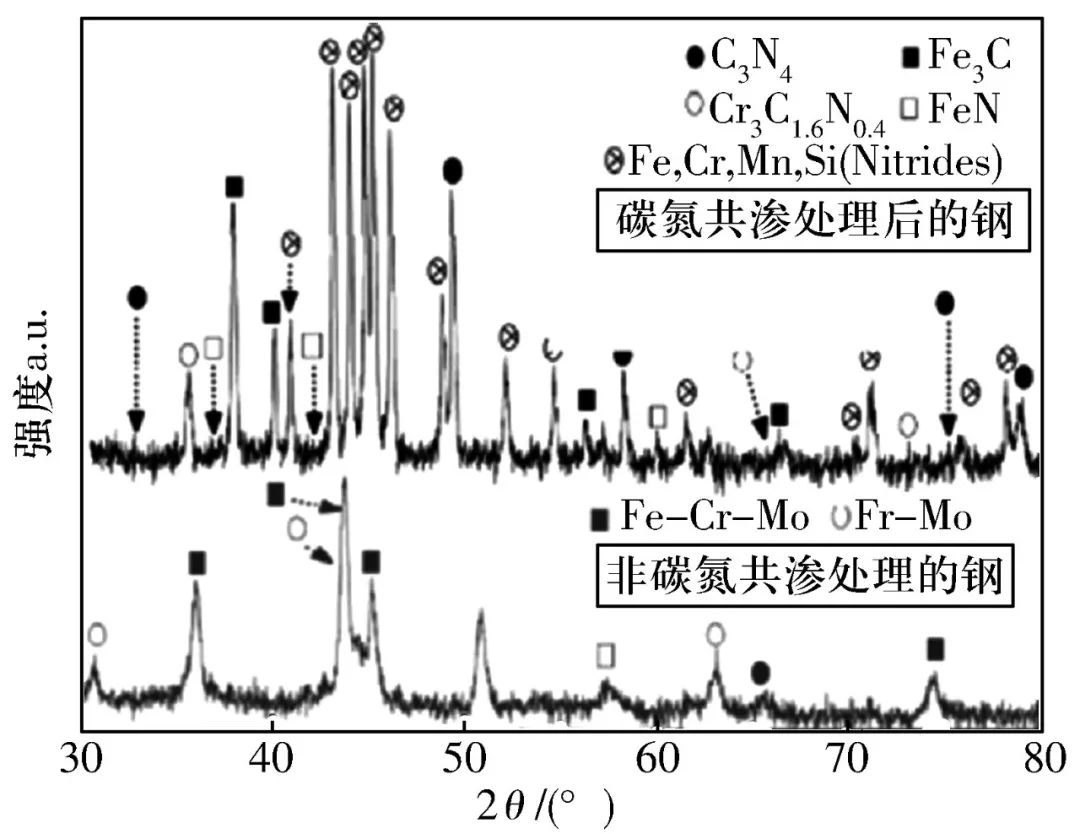
图5 渗后表层X-射线衍射图
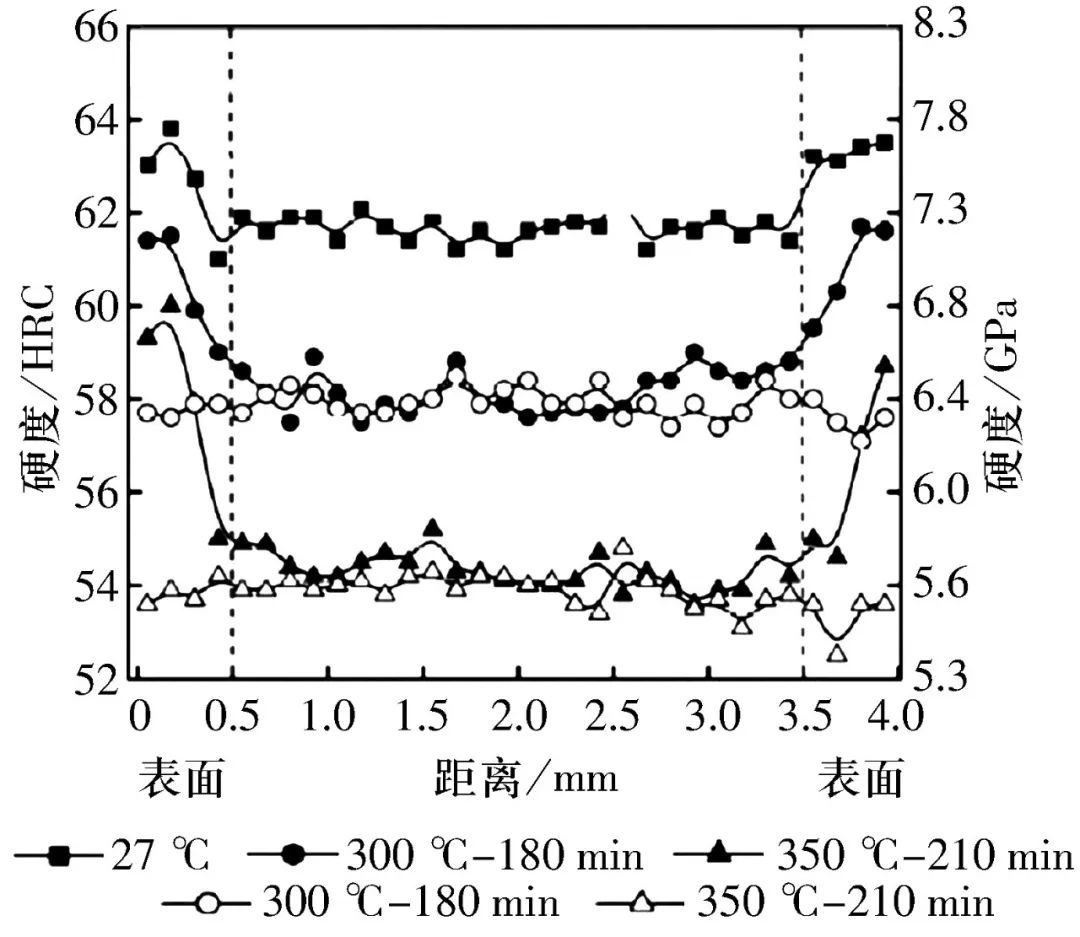
图6 碳氮共渗和非热处理钢的硬度曲线
(实心符号代表碳氮共渗,空心符号代表非碳氮共渗)
DAISUKE.S等研究了高表面氮含量碳氮共渗SUJ2的滚动接触疲劳寿命。通过控制碳氮共渗气氛的氮势使碳氮共渗后成品内圈的表面氮含量分别为0.1%和0.4%,并在人工压痕及污染润滑的条件下进行轴承疲劳寿命对比试验。人工压痕条件下,高氮含量(0.4% N)的碳氮共渗轴承疲劳寿命分别约为常规碳氮共渗(0.1%N)的2倍及普通淬回火的3倍;污染润滑条件下则为普通淬回火的2倍。高的表面氮含量提高了热处理后的残余奥氏体含量,从而提高了轴承寿命。文中还对高氮碳氮共渗不同温度回火后的压痕深度进行测量和计算,表明回火温度越高,压痕深度越浅,残余奥氏体含量越低,但未对不同温度回火后的疲劳寿命进行对比。但可以推测:对于洁净润滑的轴承,采用高的温度回火应有利于提高硬度和耐磨性。
20世纪90年代起,日本各公司积极应用这种特殊热处理技术,将其应用于污染润滑条件下工作的轴承以提高压痕起源型剥落寿命;应用于乏油润滑条件下工作的轴承以提高耐磨性;应用于异常白色组织剥落失效的轴承以防止早期剥落。
1981年,洛阳轴承研究所开展了轴承钢的碳氮共渗研究,并将碳氮共渗处理的轴承装于机床进行试验,寿命明显提高。但因种种原因被搁置,没有推广应用。进入21世纪后,国内轴承企业开始积极推广应用这一技术,尤其是在汽车变速箱轴承方面,已成为标准的热处理工艺。
4、其他化学热处理
XIE.L.C等研究了表面硬化技术和硬化层深度对AISI 8620,9310,4140钢的滚动接触疲劳性能的影响。8620及9310采用气体渗碳和真空渗碳,4140采用感应淬火,得到不同硬度和硬化层深度。接触疲劳试验表明,硬化层硬度越高、层深越厚(到613HV的最大深度小于1 mm),接触疲劳寿命越长,渗碳处理大于感应淬火,真空渗碳大于气体渗碳;而且对应于最大等效应力深度(约0.13 mm)处的硬度与疲劳寿命强相关,该处硬度越高,疲劳寿命越长。
GLOECKNER.P等将薄层氮化应用于M50,M50NiL制航空发动机球轴承,提高表面硬度及残余压应力,防止边界润滑条件下滚动接触区内微观滑动引起微剥落。
航空发动机轴承运行于高温高速及污染润滑条件下,常常因污染润滑而失效,轴承长寿命的措施之一是在常规热处理后进行离子氮化。YAGITA.K等对轴承零件用高合金钢(M50,M50NiL)的等离子氮化处理进行了研究。为保证在氮化后不出现有害的化合物层和晶间析出物,渗层中的C+N含量需小于1.7%,在430 ℃氮化10 h后进行低于回火温度的扩散处理,在不降低心部硬度的前提下保证足够的渗层深度。经以上处理后,接触疲劳试验所得的疲劳寿命L10提高了近7倍。
KOYO通过对SUJ2进行特殊热处理(碳氮共渗)开发了SH轴承,在表面获得高的硬度和一定量的残余奥氏体,使其在污染润滑条件下具有较高的寿命,且污染越严重,提高寿命的效果越显著。
5、感应加热整体热处理
感应加热淬回火有许多优点,如环保、可集成于生产线中,开、停机时间短等,一般用于表面淬火(如轮毂轴承),较少用于整体淬火。国内企业只有洛阳LYC将感应加热整体淬火用于308自动线,原因是感应加热的选择性难以保证整个零件的加热均匀性,且担心高温短时加热是否可重复性较好地控制碳在基体中的溶解量。
NTN开发了可控制钢中温度及显微组织的整体感应加热淬回火技术,其加热控制系统如图4所示。利用2支温度计同时测量套圈内外径温度,PID控制温度,基于温度测量结果的PC程序实时预测材料的性能,当钢中未溶碳化物面积到达6%~10%时停止加热,喷水淬火;根据每个回火温度下回火时间与硬度的关系,采用类似的方法控制回火温度及时间。对采用900 ℃感应加热淬火及230 ℃回火的套圈进行性能测试,与炉内加热淬回火的标准轴承相比,硬度及均匀性、耐浅层剥落及涂抹性能与标准轴承相当,尺寸稳定性及L10高于标准轴承,整个工艺每千克的CO2排放量由566 g降至318 g。
图4 带温度控制的感应加热系统示意图
NTN进一步研究了感应加热条件对轴承钢性能的影响。淬火温度为900,950,1 000 ℃,目标未溶碳化物面积为4%,8%,12%(采用不同加热时间控制),回火为180 ℃×2 h,240 ℃×43.2 s,310 ℃×36.8 s。从尺寸变化率、额定静载荷、静态断裂强度及剪切疲劳强度等性能考察不同热处理条件的影响,认为性能不低于炉内处理的最合适的热处理条件见表2。在合适热处理条件下,轴承寿命可达基本额定寿命的4倍以上。
表1 适合JIS-SUJ2的感应淬火条件